Ein Bändchenmikrofon (engl. ribbon microphone) ist ein elektroakustischer Wandler, der wie alle dynamischen Mikrofone nach dem Prinzip der Induktion arbeitet. Beim Bändchenmikrofon sind Wandlerprinzip und akustische Bauform eng verknüpft. (Zitiert aus der Wikipedia)
So ein Mikrofon wollte ich schon immer bauen. Das einfache Pinzip dahinter macht es in meinen Augen zum perfekten Selbstbau-Mikrofon!
So stöberte ich tage- und wochenlang im Netz herum, um brauchbare Informationen über den Bau zu finden. (Machen ist Silber, Vorbereitung ist Gold ;))
Hier eine kurze Liste, was man dafür benötigt:
- Gehäuse
- Magnete
- Transformator
- Hauchdünne Aluminium-Folie
- Chassis
- XLR Einbaustecker
- „Ribbon Corrugator“
Außerdem sind noch Werkzeuge und ein wenig Geschick für einen gelungenen Selbstbau von Vorteil.
Im folgenden Teil zeige ich euch, wie ich mich an die Sache rangetastet habe und welche Produkte ich dafür benutzt habe.
Das Gehäuse:
Mein erster Gedanke war: wie baue ich ein Gehäuse, das nicht zu billig aussieht und dafür auch noch wenig kostet? Ich versuchte also erst mal auf eBay ein defektes Mikrofon (vorzugsweise Bändchenmikrofon) zu ersteigern, um dieses Gehäuse zu verwenden. Allerdings hab ich recht schnell bemerkt, dass dieser Weg nicht mehr viel mit DIY zu tun hat. Davon abgesehen findet man auf fast allen Mikrofonen das Hersteller-Logo. Das möchte ich natürlich auch eher ungern. Also blieb mir nichts anderes übrig, als weiter zu suchen.
Dann bin ich irgendwann durch Zufall bei der Google Bilder-Suche auf eine erstmal witzige aber in meinen Augen sehr vernünftige Idee gestoßen: Ich benutze eine Mag-Lite als Gehäuse-Spender! Die Farbe musste natürlich Silber sein. (Wenn schon, denn schon) Natürlich reicht dafür auch ein gebrauchtes Exemplar, wenn einem Äußerlichkeiten unwichtig erscheinen 🙂
Nachdem das gute Stück bei mir eingetroffen ist, habe mit einer Metallsäge den oberen Teil der Mag-Lite über der Riffelung abgeschnitten und mir mit Klebeband die Öffnungen markiert, durch die später der Schall zum Bändchen vordringen kann.
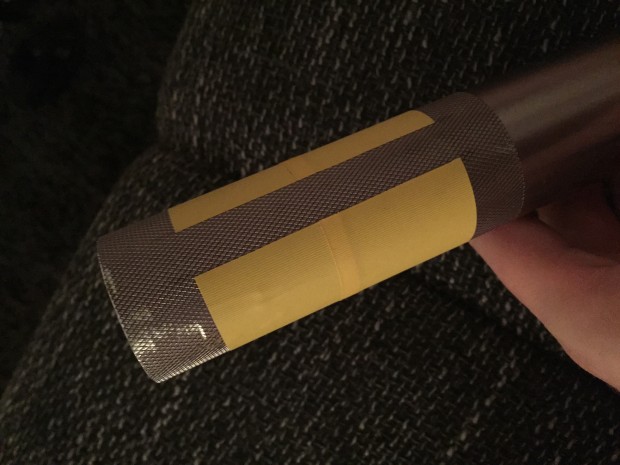
Das Gehäuse
Das klappte schon ganz gut. Die nächste Aufgabe war dann leider auch schon die schwierigste. Welches Werkzeug benötige ich, um die Öffnungen zu schneiden? Die Flex – zu groß, die Säge – kommt nicht um kurven, Fräse – zu teuer.
Da blieb nur noch eins übrig. Ich habe mir einen Dremel (Multifunktionswerkzeug) besorgt. Durch die kleinen rotierenden Scheiben, ist es kein Problem auch in die kleinsten Ecken zu kommen. Ihr fragt euch, was war daran schwierig? Es hat ewig gedauert, da das kleine Werkzeug nicht die Leistung hat wie eine oben genannte Fräse. Zudem muss man aufpassen, dass man die Scheiben beim schneiden nicht in den Schlitzen verkantet. Das ist mir ein paar mal passiert. Das Resultat daraus war, dass mir die Scheiben tatsächlich um die Ohren geflogen sind. Bis auf ein kleiner Schnitt in der Nähe meines Auges ist zum Glück nichts passiert.
Aus Fehlern lernt man, so zog ich mir endlich die nervige Schutzbrille auf.
Da ich keine Maschine bin und zum ersten Mal mit dem Dremel gearbeitet hab, sind die Kanten nicht ganz sauber geworden. Sollte ich nochmal eins bauen wollen, werde ich es wahrscheinlich fräsen lassen 😉
In meinen Pausen habe ich derweil mit meinem Fotobearbeitungsprogamm ein Layout für den sogenannten „Ribbon Motor“ erstellt. Der Ribbon Motor ist im Prinzip das fertig bestückte Chassis mit allen wichtigen Bauteilen.
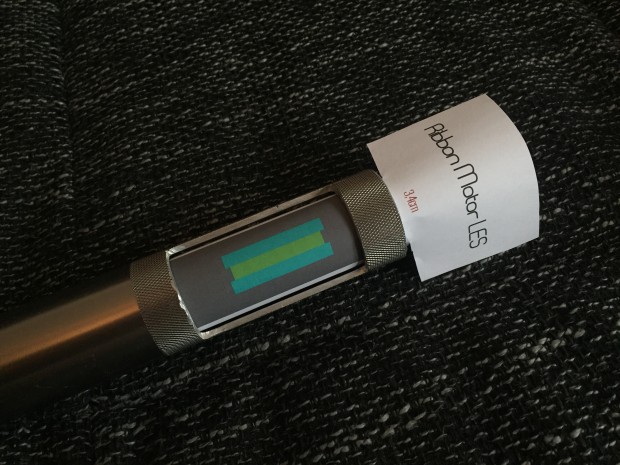
Ribbon Motor Layout
Auf dem oberen Bild kann man die Anordnung der Bauteile gut erkennen. Die blauen Balken sind Platzhalter für zwei starke Neodym-Magnete. Der grüne Balken stellt das Bändchen dar.
Der Ribbon Motor
Um das Chassis zu bauen, benötigte ich ein leicht zu bearbeitendes Material, um eventuell kleine Anpassungen für die Platzierung der Neodym-Magnete vorzunehmen. Dafür habe ich mir dann eine Platte aus Plexiglas
gekauft und auf die passende Größe zugeschnitten. Je nach Länge des Bändchens und Größe der Magneten bzw des Transformators müssen dann auch dementsprechende Aussparungen geschnitten werden. Die Länge und Breite des Chassis hängt natürlich auch von dem Gehäuse ab, für das ihr euch entscheidet.
Die Neodym-Magnete habe ich dann mit ein paar Abstandshaltern von einander getrennt und die Außenseite mit einem Schleifpapier angerauht, damit der Kleber sich besser mit dem Chassis verbindet. Ich kann einen richtig starken Kleber hier nur empfehlen, sonst besteht die Gefahr, dass die Magnete sich nach einer Zeit lösen und aufeinaner prallen. Das ist nicht nur schlecht für die Magnete, denn auch das sich später dazwischen befindende Bändchen erleidet dadurch erheblichen Schaden.
Ich habe mich daher auf den Epoxidharzkleber von UHU verlassen. Das Zeug hält bombenfest, versprochen!
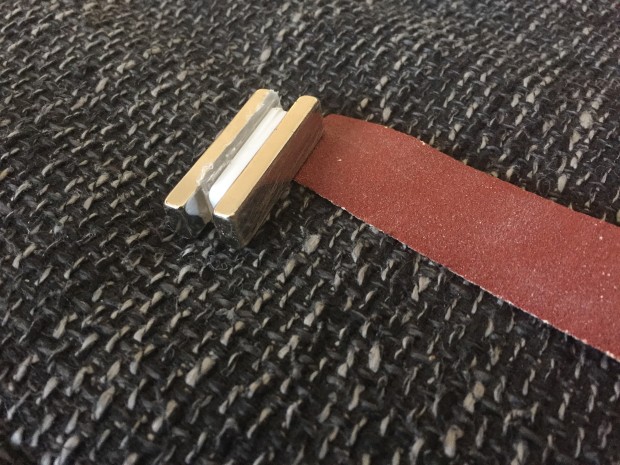
Magnete
Was den Sound betrifft, ist neben dem Bändchen und der Magnetstärke auch der Transformator von entscheidender Rolle. Da gibt es große Preisunterschiede und unterschiedliche Hersteller. Hier mal die drei wichtigsten:
- Cinemag CM-9887
- Edcor RMX-1
- Lundahl LL2912
Meine Wahl fiel auf den Edcor, da er in Deutschland leicht bei Don Audio zu besorgen und nur halb so teuer wie der Lundahl ist.
Da wir das Chassis soweit vorbereitet haben, können wir nun alle Komponenten platzieren. Den Transformator habe ich übrigens auch mit dem genannten Epoxidharzkleber fixiert.

Der Ribbon Motor
Während der Kleber Zeit bekommt, ordentlich auszuhärten, habe ich mich nun dem letzten Schritt gewidmet:
Einbau des XLR-Einbausteckers. Das war nicht weiter schwierig, allerdings musste ich einen kleinen Kompromiss eingehen. Da dieser Stecker von innen an den Schraubverschluss der Mag-Lite
angeschraubt wird, muss man darauf aufpassen, beim Zudrehen die Kabel nicht zu beschädigen.
Der Bearbeitungsschritt war auch relativ leicht. Ich habe zuerst die Mitte des Bodens mit einem Stift markiert und ein Loch von zuerst 5mm und dann 10mm Stärke vorgebohrt. Danach kam mein geliebter Stufenbohrer zum Einsatz. Mit diesem unerlässlichen Bohrer habe ich schon einige DIY Projekte realisieren können.
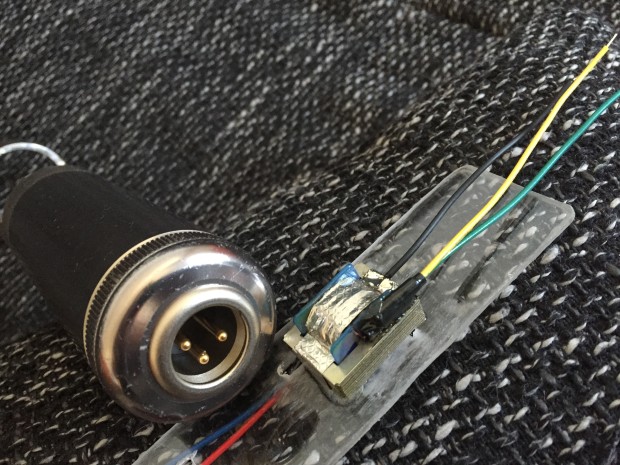
Einbaustecker und Ribbon Motor
Das Bändchen
Wer zittrige Hände hat und ungern die Nerven behält, geht jetzt lieber und beendet frühzeitig dieses Projekt. Das wäre quasi ein Projectus Interruptus 😉
Jetzt wieder ernst: ich habe beim Schneiden des Bändchens ein Exemplar zerstört, weil ich mich vermessen habe, eins ging flöten, da ich nicht ordentlich geschnitten habe und eins musste ich tauschen, da ich zum wellen des Bändchens mit dem Ribbon Corrugator nicht sauber gearbeitet habe. Das Bändchen und insgesamt das Mikrofon haben dann zwar funktioniert, der Klang war allerdings unter aller Sau!
Das Material für das Bändchen hatte in meinem Fall eine Stärke von 2,5 Mikrometern. Zum Vergleich: Das menschliche Haar hat eine Stärke von 15 Mikrometern bis zu 170 Mikrometern.
Auch für folgenden Schritt habe ich Stunden, wenn nicht sogar Tage gebraucht. Meine Aufgabe war: finde so eine dünne Folie!
Tja, wonach soll man suchen? „Dünne Alu-Folie“? „Mylarfolie“?
Es hat sich dann herausgestellt, dass ich keine passende Folie in Deutschland finden konnte – der erste Niederschlag. Dann blieb mir nichts anderes übrig, als das Netz weiter in Englisch zu durchforsten. Irgendwann kam ich auf eine lettische Seite, die alles Interessante rund um das Bändchenmikrofon anbot. Unter DIY Audio Components habe ich mir die Folie mit den Maßen von ca. 12 x 6cm für 15€ bestellt.
Als nächstes musste ein Gerät oder eine Maschine her, die mir das Bändchen faltet wie den Bald eines Akkordeons. Wieso? Das Bändchen braucht ein bisschen Spielraum, um ordentlich schwingen zu können. Wäre es zu sehr gespannt, bestünde die Gefahr, dass es reißt.
Unglaublich aber wahr: Der perfekte Ribbon Corrugator, um mein Bändchen in Form zu falten, war nichts anderes als eine Tubenpresse. Noch nicht gehört? Ich auch nicht!
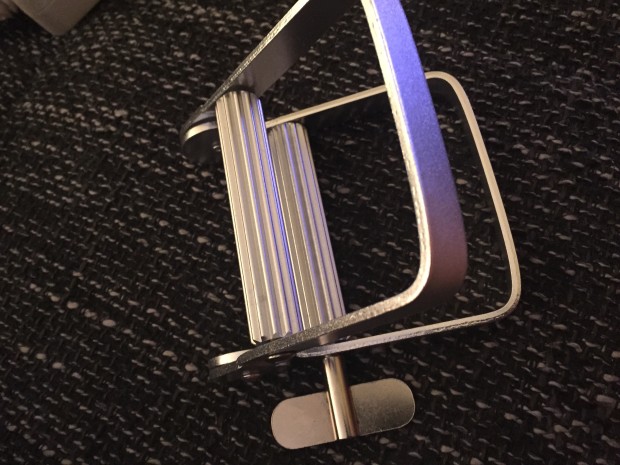
Tubepresse AKA Ribbon Corrugator
Das Bändchen Schnitt ich nun zu, sodass die Fläche zwischen den Magneten gut ausgefüllt ist, dabei aber keinen Kontakt zu den Neodym-Magneten haben darf. Sonst funktioniert der Spaß später nicht ordentlich!
Den einzigen Kontant, den das Bändchen haben muss, ist der Kontakt mit zwei Streifen selbstklebendem Kupferband, an denen die zwei Eingangskäbelchen des Transformators gelötet werden.
Nun habe ich das zugeschnittene Bändchen in ein gefaltetes Papier reingelegt, sodass die Kante des Bändchens an der inneren Kante des Papiers liegt. Danach wurde das „Werkstück“ durch die Tubenpresse gedreht, wobei darauf zu achten war, dass das Papier sich nicht selbstständig macht und mit der Hand gerade durchgeführt wird.
Das Bändchen darf nicht zu straff gespannt werden, da die Wellen sonst wieder „ausgebügelt“ sind. Gerade so viel, dass es nicht durchhängt, nicht weiter! Mit den Fingern kann man das Bändchen allerdings nicht spannen. Ich habe dafür einfach eine Zahnstocher benutzt, den ich in Alkohol getränkt habe. Durch die Flüssigkeit, bleibt das Bändchen am Zahnstocher leicht kleben. Das reicht für diesen Vorgang völlig aus!
Um das Bändchen nun im Ribbon Motor zu befestigen, habe ich mir aus Plexiglas kleine Gegenstücke geschnitten und Löcher gebohrt, durch die ich später die Schrauben führte und auf der Rückseite mit einer Mutter vereinte.
Hier kommen nun zwei Bilder. Bild 1 zeigt mein erstes Bändchen. Wie gesagt, hatte dieses einen furchtbaren und total unbrauchbaren Klang. Wenn man die Arbeit aus Bild 1 mit dem Bändchen aus Bild 2 vergleicht, erkennt man auch warum.
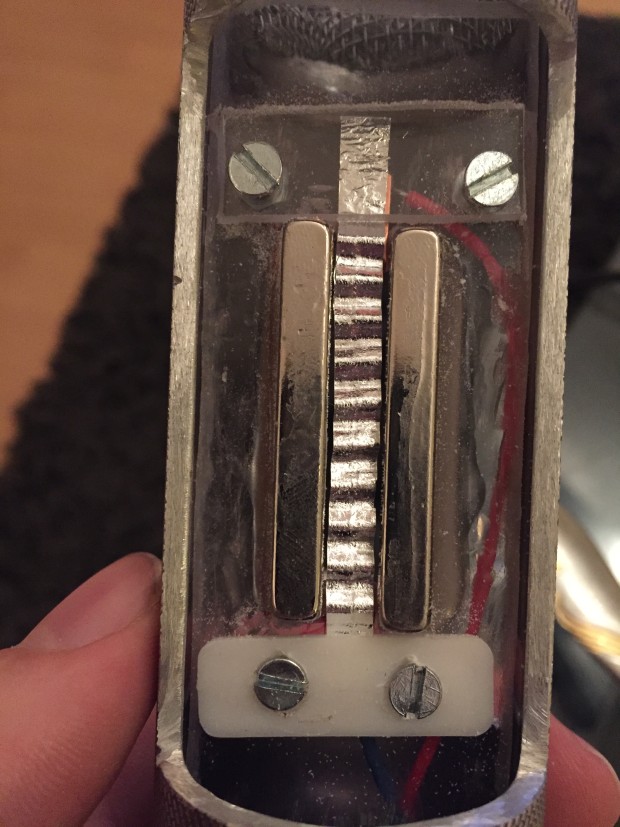
Schlechte Arbeit
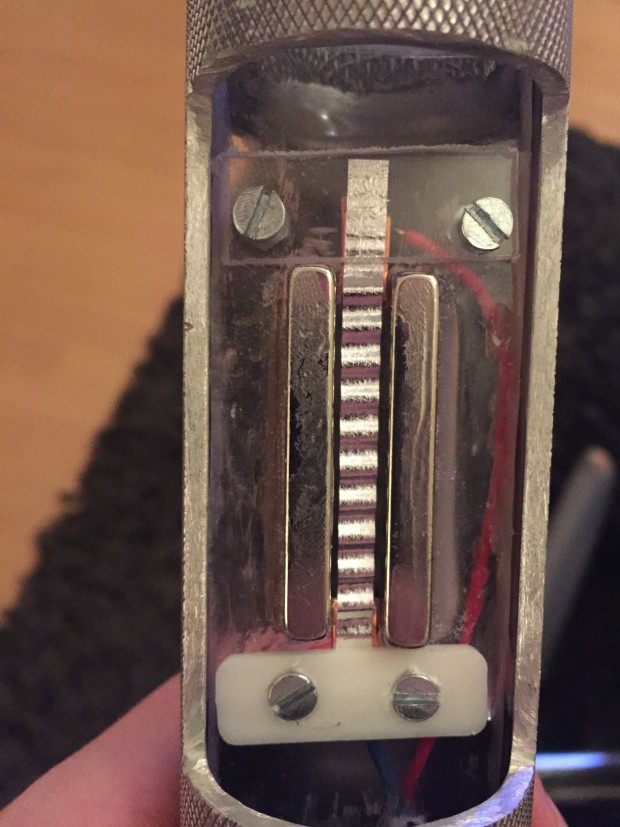
Gute Arbeit.
Jetzt ist das Mikrofon eigentlich fertig. Um das Bändchen aber ein wenig zu schützen, empfehle ich, die ausgeschnittenen Fenster mit einem Drahtgewebe zu verzieren. Generell sollte man aber bei einem Bändchenmikrofon einen Popschutz verwenden! Es erklärt sich von selbst, dass zu hoher Druck in Form von Luft auf das Bändchen treffen sollte. Beispiele wären hier: Bläser, Bassdrum, Gesang (Hier vorsichtig sein). Lautstärken an sich machen einem Bändchen aber nichts aus!
Die alles entscheidende Frage lautet: Wie klingt das Teil denn jetzt eigentlich?
Ich habe dazu zwei kurze Passagen in meinem Studio mit meiner Gitarre aufgenommen. Was die Bearbeitung angeht, habe ich nur einen leichten Lowcut bei 50Hz, einen High Boost bei 10 kHz, ein wenig Reverb, Delay und einen Kompressor eingesetzt. Alles nur leicht, damit der Sound nicht verfälscht klingt aber einen räumlicheren Eindruck macht.
Ich hoffe, ihr hattet Spaß an meiner Ausführung und wünsche euch viel Glück beim Nachbauen!
P.S.: Wenn ihr mich unterstützen wollt, klickt doch bitte auf die im Text verwendeten, orangenen Links und kauft meine Vorschläge 🙂